Feature
The latest in food manufacturing machinery innovation
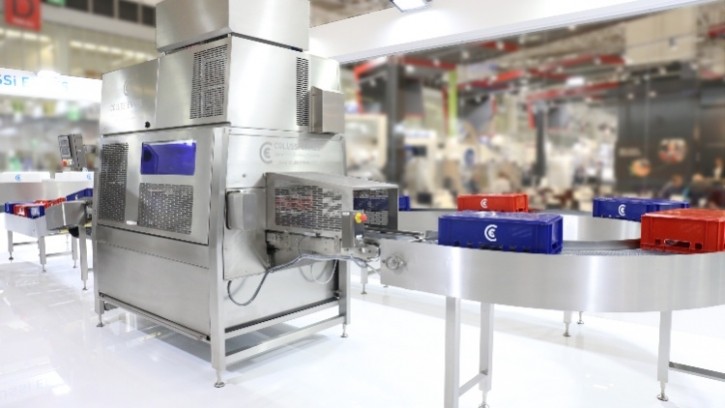
Advancements in machinery have helped transform the food and drink manufacturing industry, saving time, increasing efficiency and reducing waste.
The modern factory looks vastly different today than it did at many points in the past, the result of continuous innovation that takes place year-round. Whether focused on processing, cleaning or packaging, machinery manufacturers are in constant search of improvements that they can pass down onto their customers.
While the technology and automation found in food processing facilities is now highly advanced, the machinery featured below is emblematic of the marginal gains that innovative designers are able to achieve time and again.
Interfood partners with Colussi Ermes on new washing systems
Food processing and packaging manufacturer Interfood has linked up with Italian firm Colussi Ermes in move that allows the Buckinghamshire-based company to offer an extensive suite of washing, drying and automating solutions.
The range of Colussi Ermes equipment that Interfood now offers includes spin drying systems as well as washers for conveyor belts and filters, crates, knives and blades, racks, sticks, utensils and tote bins. The systems sit within Interfood’s thermal processing and conditioning division and can be tailored to the specific requirements of a given customer.
Operating from its head office in Italy and a satellite location in the US, Colussi Ermes is a global leader in washing systems for the food industry. With more than 50 years of experience, the firm manufactures machines that are suited to a range of food processing operations, from meat, poultry and dairy to fruit, vegetables and fish.
Interfood thermal processing and conditioning divisional manager, Steve Naylor, was particularly impressed with Colussi Ermes’ focus on minimising washing times, which helps manufacturers “substantially reduce energy consumption” throughout the cleaning process.
“Washing down equipment means downtime in processing, so by minimising washing time without reducing the all-important hygiene levels, this enables an increase in production capacity,” Naylor told Food Manufacture.
The systems also have in-built technology such as the Clean in Place (CIP) self-washing programme, which cleans the equipment to ensure the washing machines are free from contaminants.
Explaining why Interfood has linked up with Colussi Ermes, Naylor said it was important that machinery providers are in constant search of new innovations and improvements to their offering.
“Ongoing developments, both in stand-alone machines and in complete line solutions, are enabling processors to streamline their processing operations, increase capacity and thereby improve profitability,” he noted.
However, Naylor cautioned that any technology that is adopted must be suited to the specific demands of a manufacturer in order for it to achieve optimum results.
Multivac unveils three new automated packing solutions
Automated packaging machinery supplier Multivac announced the launch of three new pieces of technology last month (September 2023).
The W 510 Flowpacker, TX 620 Traysealer and Multivac Pouch Loader were all unveiled at a launch event in Swindon and are now available for order.
Designed as a more sustainable automated packaging solution, the W 510 Flowpacker allows for the improved presentation of products with a clearly defined top and bottom, such as minced meat and other foods packed in trays. Multivac states that its robust design guarantees a long lifespan, while it can be easily integrated into a full production line.
The TX 620 Traysealer is a high output tray sealing packaging machine. Possessing a small and manageable footprint, it saves space compared to its competitors and helps cut costs by reducing the reliance on labour.
Meanwhile the Multivac Pouch Loader is a semi-automatic loading solution for belt-fed chamber machines. Capable of automating the loading process, it can also reduce the need for labour on the factory floor.
Headquartered in Wolfertschwenden, Germany, Multivac has a presence in 160 countries around the world including the UK. Multivac UK product sales manager Chris Howard has been with the firm for almost four years now and believes that investing in new machinery can have numerous benefits.
He told Food Manufacture that innovation has helped boost sustainability levels within factories due to the improved energy efficiency of its technology. Customers are also able to track the energy consumption of Multivac equipment using a smart device.
“[Manufacturers] can be more profitable through higher accuracy equipment reducing giveaway, increasing yield and reducing manpower on the lines,” continued Howard.
“New equipment will also enable the manufacturers to run for longer periods having reduced downtime through increased reliability.”
TNA launches next generation packaging machinery
Meanwhile, Australian-based firm TNA has updated several of its food processing and packaging solutions with new features and capabilities.
The next generation robag 3e and auto-splice 3 are two distinct systems designed to work in tandem, with the upgrades intended to enhance how they operate. Dubbed the ‘perfect pair’, the robag 3e is a vertical form fill and seal (VFFS) packaging system and the auto-splice 3 is a complementary automatic film splicing system.
The machinery was developed to streamline the process of packing products into primary packaging, with the automatic film splicing system able to facilitate faster and smoother film changeovers.
Simon Hill, group solution specialist for packaging at TNA, told Food Manufacture that the ‘perfect pair’ provides food manufacturers with three advantages, namely increased uptime, flexibility and minimised resource use.
“These advancements in packaging technology help manufacturers optimise resource usage and achieve operational efficiencies,” added Hill.
TNA has also launched the ropac 5 – its latest iteration high performance case packer. Catering to the packaging needs of small-to-medium pillow-style bags, TNA said it is the world’s fastest case-packing system for flexible bags.
“The integration potential with existing production elements facilitates a smooth operation,” Hill explained, adding that its speed and efficiency would allow manufacturers to meet high production demands without compromising on quality.
Hill believes that TNA has proven itself a trusted partner to food manufacturers, offering “deep knowledge and experience” that help businesses thrive. However, he also emphasised the continued importance of innovation in a fast-moving sector.
“Investing in new machinery is pivotal for manufacturers aiming to maintain a competitive edge,” explained Hill.
“Furthermore, leveraging the latest technology can enhance agility, helping manufacturers to swiftly respond to fluctuating consumer demands while also enhancing the sustainability and efficiency of their production processes.”
Brillopak completes year-long improvement programme
British automated packing systems manufacturer Brillopak has also been hard at work and announced the completion of a 12-month re-engineering programme that saw the firm streamline the size and price of some of its most popular systems.
The UniPAKer, PunnetPAKer and TrayPAKer were all upgraded, with the next generation versions unveiled at the Processing and Packaging Machinery Association (PPMA) trade show in Birmingham last month. Each second-gen version is 25% cheaper and smaller than its predecessor and has a build time of less than eight weeks.
Despite the change, Brillopak states that each systems retains the same build quality, speed, consistency and repeatable pack presentation in crates and cases.
The re-engineering programme was carried out by the firm’s in-house research and development (R&D) department and focused on the combined use of new and established technologies. This allowed Brillopak to remove surplus cables and panels, simplify the frame structures, streamline the number of components and controls and increase the number of parts that are common across different products.
Brillopak technical director Peter Newman said that the experience of last year’s PPMA 2022 persuaded the Kent firm to “get back to basics” and find ways of offering better value.
“We are finding that customers don’t want more for their money; they simply want to spend less on easy to integrate machinery,” Newman explained.
“We’d like to thank our trusted partners and those who continue to collaborate with our re-engineering programme and adventure to make the best pick, place and packing systems affordable to all: Omron, Norgren, Wenglor, SLPlastics, Underwoods, Vmeca.”
Third generation FoodJet and Xylem pizza sauce machine revealed
FoodJet has launched its third generation pizza sauce depositing machine, in partnership with UK technology firm Xylem.
The FoodJet MDL pizza sauce depositor is a high-capacity machine that eliminates the need for manual labour in sauce depositing. Hundreds of nozzles print the sauce accurately on the bases, ensuring that the precise shape and weight in sauce gets deposited.
The first edition of the MDL pizza sauce depositor was launched in 2019 following an initial collaboration between the two firms - the Xylem Jabsco 28200 Series flexible impeller pumps are used on the latest update to ensure the tomato sauce droplets remain uniform throughout the process.
Xylem flexible impeller pumps have the ability to pump a range of viscosities and can handle soft solids with a maximum diameter of 4mm. Each pump is easy to service and maintain thanks to their CIP capabilities, while they also meet European and US food safety standards for hygienic applications.
Head of sales and marketing at FoodJet, Dirk Schindler, said that the MDL pizza sauce depositor is “completely different” from any of the alternatives on the market, in part due to the use of Xylem technology.
Schindler elaborated: “Our world-first technology has an array of nozzles that can be activated individually, and operators can choose the volume of sauce each nozzle deposits depending on the application specifications.”
Discussing the partnership with Xylem, he said that its pumps had “exceeded expectations”, allowing its machines to create “perfect pizzas, every time”.
Edwin de Haan, industry sales manager at Xylem, echoed the goodwill expressed by Schindler, adding that the firm is “proud to partner with them on this innovative solution”.
On the quality of the Xylem’s design, de Haan explained: “[Our] hygienic Jabsco flexible impeller pumps have been designed to meet stringent food contact regulations in multiple markets, making us the only pump provider in the world to offer food safe products that meet regional standards on a global scale.”